As a tape industry professional, I’ve seen firsthand how crucial packaging efficiency is for businesses. A tape packing machine may seem like a small part of the process, but when you’re dealing with high-volume operations, it’s often the little things that make the biggest impact on your bottom line. Over the years, I’ve learned that investing in the right #tape packing machine can save thousands—not just in immediate costs, but in long-term gains too.
In this article, I’ll walk you through why upgrading to a modern tape packing machine can save your business significant amounts of money and provide some real-world examples based on my own experience running a tape company.
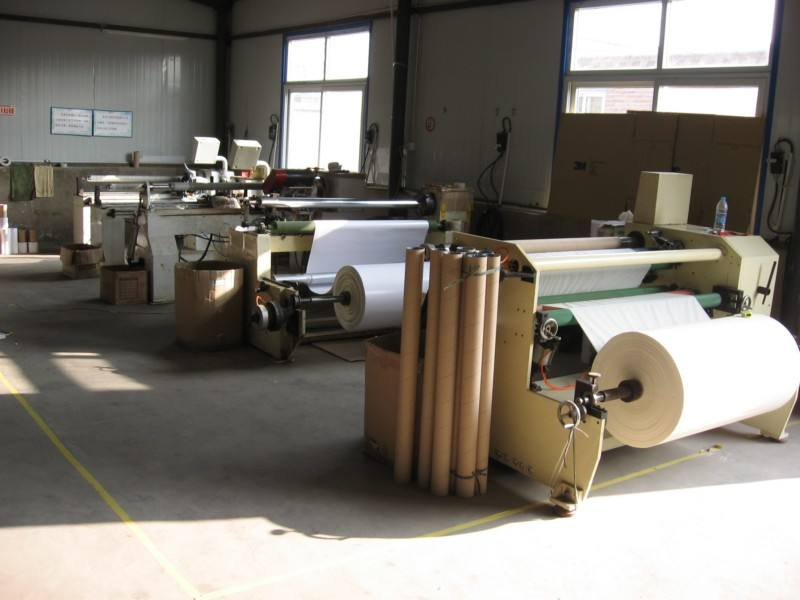
The Hidden Costs of Manual or Outdated Packing Processes
When I first started out in the tape business, we were using manual packing methods and older machines that were on their last legs. At the time, we thought this was the cheaper option. But once we started really looking into the numbers, the hidden costs became glaringly obvious.
Labor Costs: Time is Money
One of the biggest costs of manual packing is labor. When you’re running a factory, every second counts, and manual packing processes eat up time like you wouldn’t believe. Not only that, but the longer an employee spends manually put the PVC film on the tape and put it inthe shrinking machine, the higher your labor costs.
I remember one year where we had a huge order come in, and we ended up hiring extra staff just to keep up with demand. It wasn’t until later that I realized how much money we were throwing away. A tape packing machine could’ve done the same job in One fifth time, saving us over 10 thousands in labor costs over the half year.
Material Waste: More Tape, More Money
Older machines—or even manual packing tape application—tend to use far more PVC shrinking film than necessary. When employees are packing tape by hand, they often overcompensate by using extra layers of shrinking film to make sure the final result are good. Sometime needs packing again if shrinking effect is terrible, which can result in product damage or package returns.
In my own experience, switching to a modern tape packing machine reduced our shrinking film consumption by around 5%. It doesn’t sound like a lot, but over 20 thousands pcs of shrinking film per day, it adds up quickly. I’d estimate we saved thousands of dollars just by reducing material waste.
Downtime and Maintenance: The Silent Killer
If you’ve ever dealt with an old packing machine, you know that downtime is inevitable. There’s nothing more frustrating than a machine breaking down in the middle of a big order. Not only do you have to pay for repairs, but you’re also losing time, which equals lost revenue.
Stable is the most important for automatic tape packing machine,I found out some of machinery manufacture using unique design —– Round turntable design,More stable than linear packaging machines, reducing after-sales.Using modern tape packing machine with fewer maintenance needs and better parts made a world of difference in tape production flow.
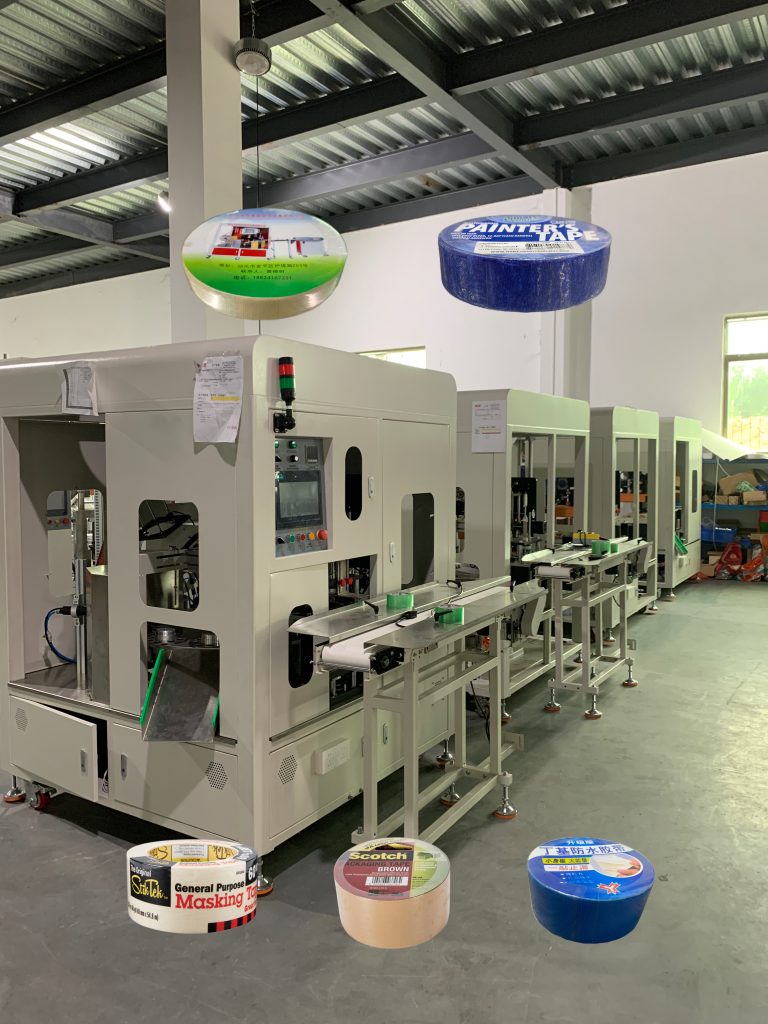
How Modern Tape Packing Machines Reduce These Costs
Once we decided to invest in a new tape packing machine, the cost savings were almost immediate.
Automation: Speed and Efficiency
Modern tape packing machines are incredibly efficient. They can packing tape faster than any human could, which means you can process more orders in less time. We saw an immediate boost in our throughput once we switched. What used to take hours now took a one fifth of the time.
One of my best decisions was investing in an automated machine that could handle high-speed production lines. We used to have ten people on the line—three of them just for packing tape. With the new tape packing machine, we were able to reduce that to one person monitoring the machine, and we doubled our packaging output.
Precision tape packing : Consistency That Saves
Not only are these machines fast, but they’re also incredibly precise. Every tape gets the exact amount of pvc shrinking film needed—no more, no less. This means you’re saving film on every adhesive tape, and your packaging is consistent,more Beautiful which keeps customers happy and reduces returns.
Our packing film consumption dropped significantly. We no longer had employees over-packing film, and the consistent seals meant fewer packages arrived damaged.
Real-World Savings: A Personal Case Study
Let me give you a quick breakdown of how much we saved after upgrading to a modern tape packing machine:
Labor Savings: By automating the packing process, we reduced our labor costs by about 50%. Fewer people were needed on the line, and those that remained could focus on more skilled tasks.
Packing film Savings: We used roughly 10% less packing film thanks to the machine’s precision application. Over the course of a year, this translated into thousands of dollars in packing film savings alone.
Maintenance and Downtime: Our old machines were constantly breaking down, costing us not just in repairs but in lost time. With the new tape packing machine, maintenance costs dropped significantly, and the machine was far more reliable, with fewer interruptions.
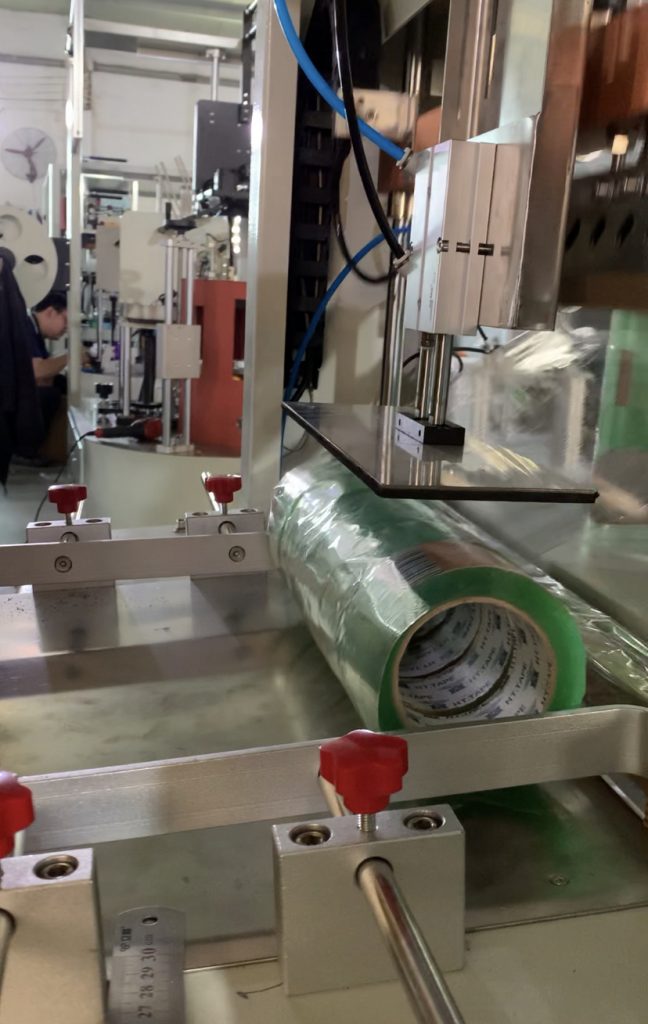
Additional Benefits Beyond Cost Savings
While saving money is the primary focus, there are other perks to upgrading your tape packing machine that can benefit your business.
Improved Product Presentation
When a package is perfect-sealed, it not only protects the product inside, but it also looks more professional. In my experience, customers appreciate the consistent and clean tape packing lines that an industrial tape packing machine provides. If your packages look sloppy or insecure, it reflects poorly on your business.
Increased Customer Satisfaction
Fewer returns mean happier customers. With our new tape packing machine, we saw a drop in damaged goods during shipping because the tape was applied evenly and securely. Our customers noticed, and we saw an increase in repeat business as a result.
Scalability
One of the best things about our new machine was how easy it made scaling our operations. As demand grew, we didn’t need to hire more people—we just ran the machine longer. Having this capability allowed us to take on larger orders without worrying about capacity issues.
Choosing the Right Tape Packing Machine for Your Business
So, what should you look for when choosing a tape packing machine for your operation? Here are a few key considerations:
Automation Level: Do you need a fully automated system, or will a semi-automatic machine suffice? This depends on the volume of packaging you handle.
Tape Compatibility: Make sure the machine you choose can handle the types and widths of tape you use in your packaging processes.
Production Capacity: Consider how many pcs per minute the machine can packing and whether it aligns with your production goals.
Maintenance and Support: Choose a supplier who provides excellent support and has a good track record for machine reliability. When machines need parts or repairs, you want to ensure you can get them quickly.
Conclusion: The Time to Invest is Now
Investing in an industrial tape packing machine might seem like a big upfront cost, but I can tell you from experience that the long-term savings are worth it. You’ll save on labor, tape, and maintenance, while increasing your production speed and improving your product packaging.
If you’re still relying on manual processes or outdated machines, now is the time to make the switch. Trust me, your business—and your bottom line—will thank you for it.